Skuteczne zabezpieczenie antykorozyjne dla rur stalowych
Praktycznie każdy system wewnętrznej infrastruktury i podtrzymywania życia budynków mieszkalnych, budynków komunalnych i komercyjnych lub obiektów przemysłowych jest ogólnie rozwiniętą siecią rurociągów łączących te lub inne obiekty systemu w określonej kolejności.
W wielu przypadkach, na przykład w rurociągu gazu regeneracji, gorącej i zimnej wody w kale lub przewodów, a także jako systemy ogrzewania oraz wentylacji stosowane ziemią antenowy lub wewnętrznej wyściółki metalowych rur o różnych średnicach i rozmiarach.
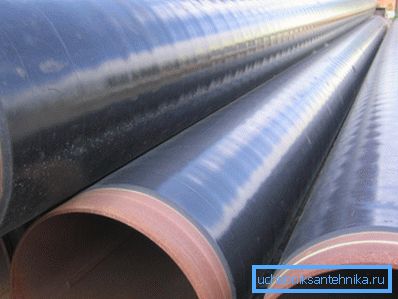
W zależności od trybu pracy i warunków środowiskowych, metalowe rury mogą być narażone na różne niekorzystne czynniki przez długi czas podczas pracy. Aby rozwiązać ten problem, specjalnie opracowano kompleksową ochronę rurociągów przed korozją zgodnie z SNiP 2.03.11-85 "Ochrona konstrukcji budowlanych przed korozją".
Metody radzenia sobie z korozją
Aby pomóc czytelnikowi dowiedzieć się, jak zapewnić maksymalną wytrzymałość rurociągu, w tym artykule przyjrzymy się niektórym opcjom aktywnej i pasywnej ochrony wyrobów metalowych, które składają się na usługi inżynierii rurociągów.
Również tutaj będzie szczegółowa instrukcja, która wyszczególnia podstawowe zasady wdrażania ochrony antykorozyjnej wyrobów metalowych przeznaczonych do pracy w agresywnych warunkach.
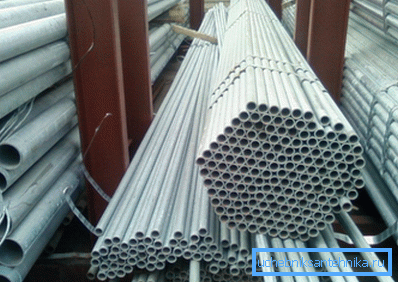
Klasyfikacja złośliwych czynników
Jak wspomniano powyżej, charakter i zakres wpływów zewnętrznych zależy w dużym stopniu od konkretnych warunków pracy, takich jak miejsce układu rur, składu chemicznego gleby, średniej temperatury i wilgotności względnej otoczenia, w sąsiedztwie źródła prądu stałego, etc.
Zgodnie z mechanizmem występowania i stopniem szkodliwego oddziaływania wszystkie szkodliwe czynniki można podzielić na kilka typów.
- Korozja atmosferyczna występuje, gdy żelazo oddziałuje z parą wodną, która jest zawarta w otaczającym powietrzu, a także w wyniku bezpośredniego kontaktu z wodą podczas opadów. W trakcie reakcji chemicznej powstaje tlenek żelaza, a dokładniej zwykła rdza, która znacznie obniża wytrzymałość produktów metalowych, az biegiem czasu może doprowadzić do ich całkowitego zniszczenia.
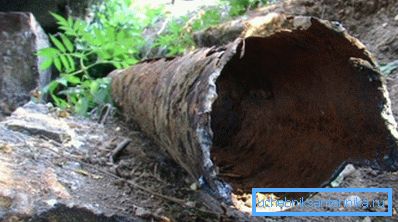
- Korozja chemiczna wynika z interakcji żelaza z różnymi aktywnymi związkami chemicznymi (kwasy, alkalia itp.). Jednocześnie zachodzące reakcje chemiczne prowadzą do powstawania innych związków (soli, tlenków itp.), Które podobnie jak rdza stopniowo niszczą metal.
- Korozja elektrochemiczna występuje, gdy produkt żelaza znajduje się w środowisku elektrolitowym przez długi czas (wodny roztwór soli o różnych stężeniach). W tym samym czasie na metalowej powierzchni, pomiędzy którymi płynie prąd elektryczny, tworzą się obszary anodowe i katodowe. W wyniku emisji elektrochemicznej cząstki żelaza są przenoszone z jednego miejsca na drugie, co prowadzi do zniszczenia produktu metalowego.
- Narażenie na ujemne temperatury gdy rury są używane do transportu wody, powoduje to jej zamarznięcie. Po przejściu w stały stan skupienia, sieć krystaliczna tworzy się w wodzie, w wyniku czego jej objętość wzrasta o 9%. Będąc w zamkniętej przestrzeni, woda zaczyna naciskać na ściany rury, co ostatecznie prowadzi do ich pęknięcia.
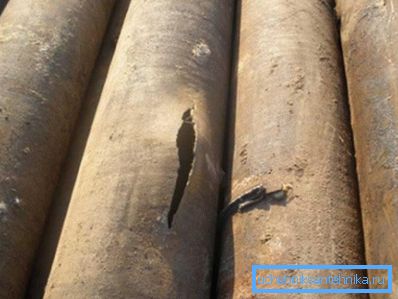
Zwróć uwagę! Znacząca różnica średnich rocznych i średnich temperatur dziennych prowadzi do znacznych wahań całkowitej długości rurociągu, które są spowodowane liniowym rozszerzeniem cieplnym materiału. W celu uniknięcia pęknięcia rur i uszkodzenia konstrukcji wsporczych, kompensatory termiczne muszą być zainstalowane w pewnej odległości od linii.
Analiza gleby
Aby wybrać najbardziej skuteczną metodę ochrony, konieczne jest posiadanie dokładnych informacji o charakterze środowiska i specyficznych warunkach eksploatacji stalowego rurociągu. W przypadku układania linii wewnętrznej lub lotniczej informacje te można uzyskać na podstawie subiektywnych obserwacji, a także na podstawie średniorocznego reżimu klimatycznego dla tego regionu.
W przypadku układania podziemnego rurociągu, odporność na korozję i trwałość metalu zależy w dużej mierze od parametrów fizycznych i składu chemicznego gleby, więc zanim wykopać rów z ich rąk, należy przekazać próbki gleby do analizy do specjalistycznego laboratorium.
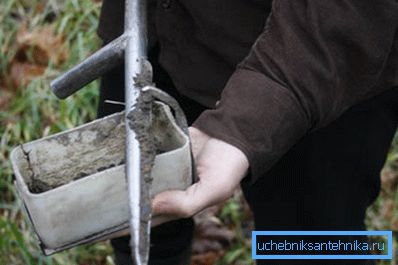
Najważniejszymi wskaźnikami, które należy wyjaśnić w procesie analizy, są następujące cechy gleby:
- Skład chemiczny i stężenie soli różnych metali w wodzie gruntowej. Gęstość elektrolitu i przepuszczalność elektryczna gleby w dużej mierze zależy od tego wskaźnika.
- Jakościowe i ilościowe wskaźniki kwasowości gleby, które mogą powodować zarówno utlenianie chemiczne, jak i korozję elektrochemiczną metalu.
- Odporność elektryczna na glebę. Im niższa wartość rezystancji elektrycznej, tym bardziej metal ulega zniszczeniom powodowanym przez emisję elektrochemiczną.
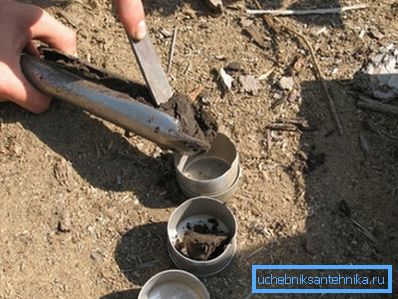
Wskazówka! Aby uzyskać obiektywne wyniki analizy, próbki gleby muszą zostać usunięte z warstw gleby, w których przebiegnie rurociąg.
Zabezpieczenie przed niską temperaturą
W przypadku podziemnego lub powietrznego układania sieci wodociągowych i kanalizacyjnych, najważniejszym warunkiem ich nieprzerwanego działania jest zabezpieczenie rur przed zamarzaniem i utrzymanie temperatury wody na poziomie nie niższym niż 0 ° С w zimnych porach roku.
Aby zmniejszyć negatywny wpływ czynnika temperaturowego na środowisko, stosowane są następujące rozwiązania techniczne:
- Ułożenie podziemnego rurociągu na głębokości przekraczającej maksymalną głębokość zamarzania gleby dla regionu.
- Izolacja cieplna linii powietrznych i podziemnych przy użyciu różnych materiałów o niskim przewodnictwie cieplnym (wełna mineralna, segmenty piankowe, tuleje polipropylenowe).
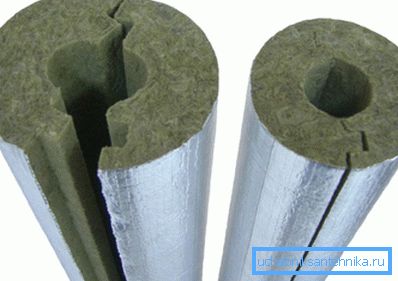
- Wypełnianie wykopu rurociągowego materiałem sypkim o niskiej przewodności cieplnej (keramzyt, żużel węglowy).
- Odwodnienie sąsiednich warstw gleby w celu zmniejszenia jej przewodności cieplnej.
- Układanie podziemnych mediów w sztywnych zamkniętych skrzyniach wykonanych ze zbrojonego betonu, które zapewniają szczelinę powietrzną między rurą a ziemią.
Najbardziej postępową metodą zabezpieczania rur przed zamarzaniem jest użycie specjalnej obudowy składającej się z powłoki wykonanej z materiału termoizolacyjnego, wewnątrz której układany jest elektryczny element grzejny.
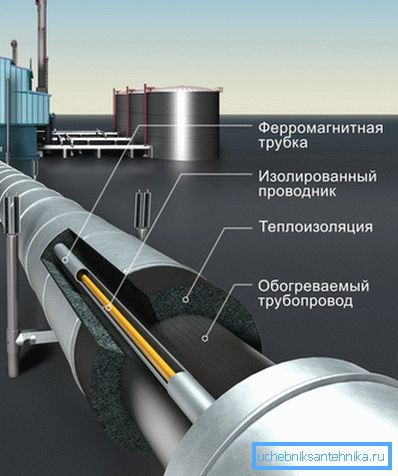
Zwróć uwagę! Głębokość przemarzania dla każdego regionu, a także sposób jego obliczania jest regulowany przepisami ciach 2.02.01-83 * „Fundamenty budowli» i SNIP 23-01-99 * Budynek klimatologii.
Zewnętrzna powłoka hydroizolacyjna
Najczęstszym sposobem zwalczania korozji metali jest nanoszenie cienkiej warstwy trwałego wodoodpornego materiału ochronnego na jej powierzchnię. Najprostszym przykładem zewnętrznej powłoki ochronnej jest konwencjonalna wodoodporna farba lub emalia, na przykład ochrona rury gazowej przechodzącej przez powietrze jest zawsze przeprowadzana za pomocą odpornej na warunki atmosferyczne żółtej emalii.
Podziemne instalacje wodociągowe i gazociągi są z reguły montowane z rur wstępnie powlekanych na zewnątrz grubą warstwą masy bitumicznej, a następnie owijane ciężkim papierem technicznym. Powłoki wykonane z materiałów kompozytowych lub polimerowych są również bardzo skuteczne.
Metalowe elementy podziemnych sieci kanalizacyjnych od wewnątrz i na zewnątrz pokryte są grubą warstwą zaprawy cementowo-piaskowej, która po zestaleniu tworzy jednolitą monolityczną powierzchnię.
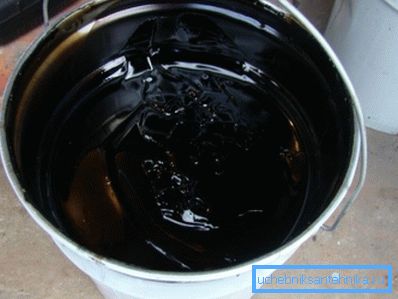
Aby niezależnie wybrać odpowiedni materiał do zewnętrznej powłoki, należy wiedzieć, że w celu zapewnienia maksymalnej ochrony, musi on jednocześnie posiadać kilka cech.
- Po wyschnięciu powłoka lakierniczo-lakierowa powinna mieć ciągłą jednorodną powierzchnię o wysokiej wytrzymałości mechanicznej i absolutnej odporności na wodę.
- Folia ochronna z materiału hydroizolacyjnego, o określonych właściwościach, musi być elastyczna i nie zapadać się pod wpływem wysokich lub niskich temperatur.
- Materiał wyjściowy do powlekania powinien mieć dobrą płynność, wysoką zdolność krycia, jak również dobrą przyczepność do powierzchni metalu.
- Innym wskaźnikiem jakości materiału izolacyjnego jest to, że musi to być absolutny dielektryk. Dzięki tej właściwości zapewnione jest niezawodne zabezpieczenie rurociągów przed prądami błądzącymi, które zwiększają niekorzystne skutki korozji elektrochemicznej.
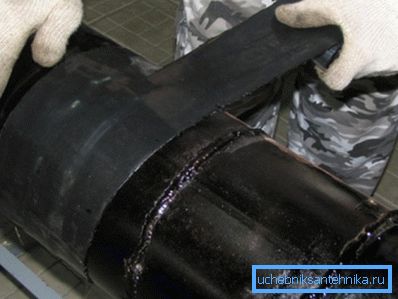
Wskazówka! Najskuteczniejsze rozwiązania izolowania metalu ze środowiska są uważane za kompozycje oparte na żywicach bitumicznych, dwuskładnikowych polimerowych kompozycjach, a także walcowanych polimerowych materiałach na bazie samoprzylepnej.
Aktywna i pasywna ochrona elektrochemiczna
Podziemne instalacje są bardziej podatne na pojawienie się korozji niż powietrze i wewnętrzne rurociągi, ponieważ stale znajdują się w środowisku elektrolitu, który jest roztworem soli zawartych w składzie wód podziemnych.
W celu zminimalizowania niszczącego efektu powodowanego przez reakcję żelaza z roztworem elektrolitu z solą wodną, stosuje się aktywne i pasywne metody ochrony elektrochemicznej.
- Aktywna metoda katodowa polega na kierunkowym ruchu elektronów w obwodzie stałoprądowym. Do jego realizacji, rurociąg jest podłączony do ujemnego bieguna źródła prądu stałego, a pręt uziemiający anodę jest podłączony do dodatniego bieguna, który jest zakopany w ziemi w pobliżu. Po pobudzeniu obwód elektryczny zamyka się przez elektrolit gruntowy, w wyniku czego swobodne elektrony zaczynają przemieszczać się od pręta gruntowego do rurociągu. W ten sposób elektroda uziemiająca stopniowo zapada się, a uwolnione elektrony zamiast rurociągu reagują z elektrolitem.
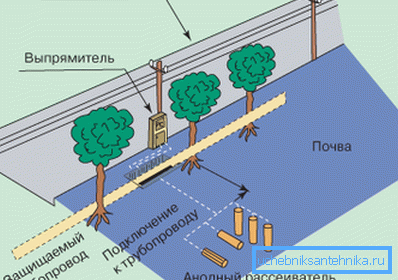
- Pasywna ochrona protektorowa rurociągów jest to, że obok żelaza, elektroda z bardziej elektroujemnego metalu, takiego jak cynk lub magnez, jest umieszczana w ziemi i elektrycznie połączona ze sobą poprzez kontrolowane obciążenie. W ośrodku elektrolitycznym tworzą one parę galwaniczną, która w trakcie reakcji, podobnie jak w poprzednim przypadku, powoduje ruch elektronów z ochraniacza cynku na chroniony rurociąg.
- Zabezpieczenie przed odwadnianiem elektrycznym Jest to również metoda pasywna, polegająca na podłączeniu rurociągu do obwodu uziemiającego, wykonanego zgodnie z EMP. Metoda ta pomaga pozbyć się prądów błądzących i jest stosowana w przypadku lokalizacji rurociągu w pobliżu elektrycznej sieci transportu lądowego lub kolejowego.
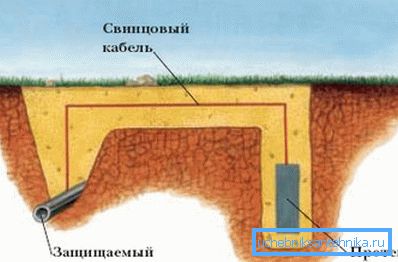
Zwróć uwagę! Dobrym przykładem ochrony biernego protektora jest dobrze znana powłoka cynkowa z produktów żelaznych lub, po prostu, cynkowanie galwaniczne.
Wniosek
Każda z powyższych metod ma swoje zalety i wady, dlatego powinny być stosowane w zależności od konkretnych warunków, które powstały. Podsumowując, należy stwierdzić, że niezależnie od wybranej metody, koszt naprawy i wymiany rurociągu będzie znacznie droższy niż koszt najbardziej złożonej i czasochłonnej ochrony.
Aby uzyskać więcej informacji, możesz obejrzeć film wideo w tym artykule lub przeczytać podobne materiały na naszej stronie internetowej.